Sobre Gyform
DESCUBRE MáS SOBRE GYFORM
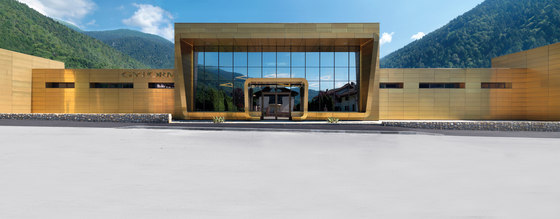
Company Profile
The history of Gyform was born in Vigo Rendena, in Trentino in the late 50’s with the initiative of Mr. Guido Gasperi. From the beginning, manufacturing was based on well-defined guiding principles: quality and tradition, as well as continuous innovation and vision towards the future. Thanks to an elegant fabrication of sofas and armchairs, Gyform has become a benchmark for high- end furnishings all over the world. Gyform uses a working method that preserves the ancient culture of master upholsterers and combines it with the continuous technological innovation of the production lines. Today, Gyform’s factory covers a total area of 10.000 square meters where, in addition to the factory floor, there is an area devoted to research and development and product engineering prototypes, as well as a showroom available to staff and trade professionals.
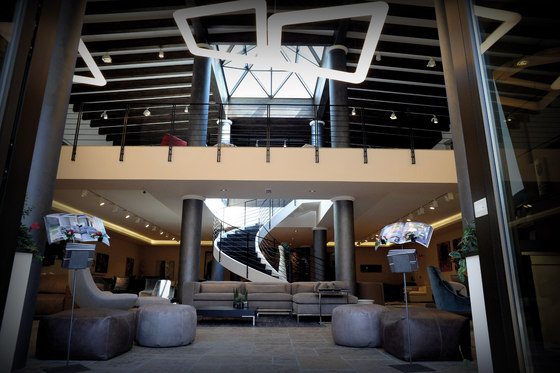
Company Showroom
The year 2013 saw the opening of a new showroom spanning 1,000 square meters on two floors with meeting rooms, eating ame- nities, as well as two new warehouses for storing of leather which adds another 1,500 meters which adds 5,000 square meters of covered area that already exist. Classified as “zero energy”, the new facility is able to use the least amount of energy for its operation following a highly developed construction criteria which makes it sustainable. Inside, the interaction of architecture, art and design produce a superb exhibit. The visitor is captivated by the inviting atmosphere, through the use of natural materials such as wood and stone. An elegant setting to display the collections, which also provides a meeting and training center for clients, architects and designers.
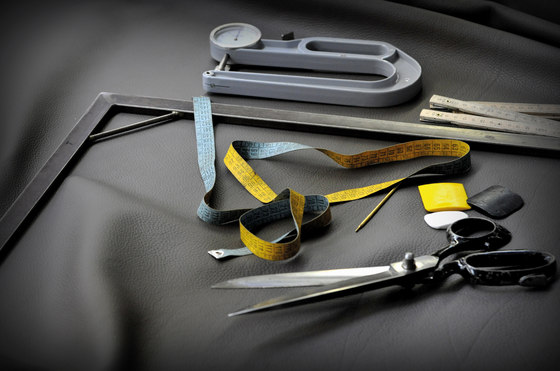
Production Process
In Italy and abroad, Gyform is synonymous with quality. Every detail is precisely designed, and each component is made from the highest quality materials. The structures of sofas are exclusively made of solid beech, poplar, pine or spruce, all with multi-layered special support and assembled by hand to ensure durability. Fabrics and leathers are meticulously checked by experts to exclude any imperfections and to be prepared for cutting operations. Once cut, each piece is again supervised for consistency and quality control. The cut segments are then sent to the sewing depart- ment, where highly skilled staff take care of the finishing details. In the assembly department the product takes its final form and undergoes a thorough final inspection before being sent to the shipping section. Each material used in the fabrication is subjected to various tests to determine the resistance and the durability. A careful inspection is also carried out from the ecological point of view, with the limitation and/or elimination of chemical contaminants.
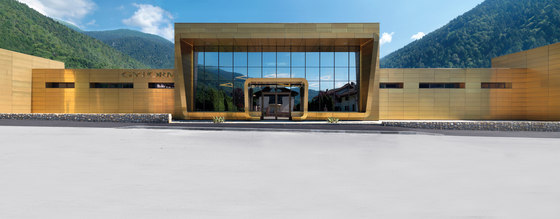
Company Profile
The history of Gyform was born in Vigo Rendena, in Trentino in the late 50’s with the initiative of Mr. Guido Gasperi. From the beginning, manufacturing was based on well-defined guiding principles: quality and tradition, as well as continuous innovation and vision towards the future. Thanks to an elegant fabrication of sofas and armchairs, Gyform has become a benchmark for high- end furnishings all over the world. Gyform uses a working method that preserves the ancient culture of master upholsterers and combines it with the continuous technological innovation of the production lines. Today, Gyform’s factory covers a total area of 10.000 square meters where, in addition to the factory floor, there is an area devoted to research and development and product engineering prototypes, as well as a showroom available to staff and trade professionals.
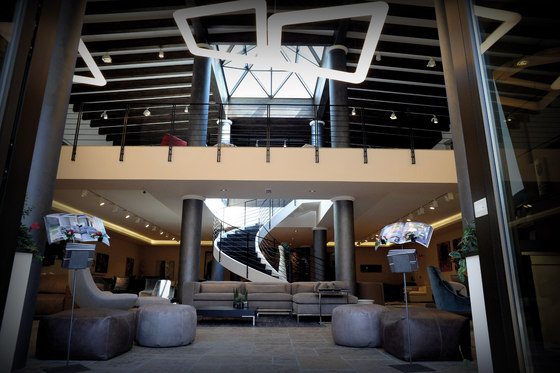
Company Showroom
The year 2013 saw the opening of a new showroom spanning 1,000 square meters on two floors with meeting rooms, eating ame- nities, as well as two new warehouses for storing of leather which adds another 1,500 meters which adds 5,000 square meters of covered area that already exist. Classified as “zero energy”, the new facility is able to use the least amount of energy for its operation following a highly developed construction criteria which makes it sustainable. Inside, the interaction of architecture, art and design produce a superb exhibit. The visitor is captivated by the inviting atmosphere, through the use of natural materials such as wood and stone. An elegant setting to display the collections, which also provides a meeting and training center for clients, architects and designers.
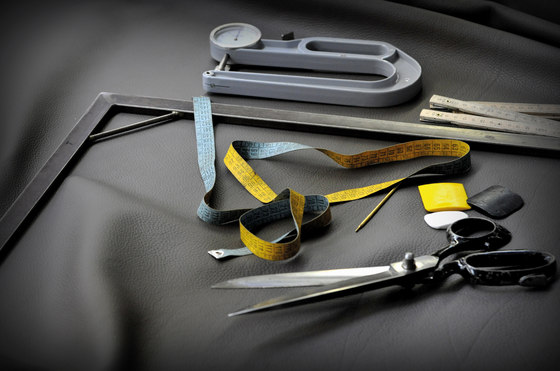
Production Process
In Italy and abroad, Gyform is synonymous with quality. Every detail is precisely designed, and each component is made from the highest quality materials. The structures of sofas are exclusively made of solid beech, poplar, pine or spruce, all with multi-layered special support and assembled by hand to ensure durability. Fabrics and leathers are meticulously checked by experts to exclude any imperfections and to be prepared for cutting operations. Once cut, each piece is again supervised for consistency and quality control. The cut segments are then sent to the sewing depart- ment, where highly skilled staff take care of the finishing details. In the assembly department the product takes its final form and undergoes a thorough final inspection before being sent to the shipping section. Each material used in the fabrication is subjected to various tests to determine the resistance and the durability. A careful inspection is also carried out from the ecological point of view, with the limitation and/or elimination of chemical contaminants.
DESCUBRE MáS SOBRE GYFORM