Silent Partner
Texto por Frame Publishers
Holanda
08.08.13
Fantoni Group’s innovations in acoustic panelling please the eye as well as the ear, thanks to the firm’s focus on a design-led approach and an integrated manufacturing strategy.
Let’s face it, acoustic panelling is probably the last thing you think about as you enjoy a meal in a restaurant or make your way through a busy airport – but an unsung architectural element like this one can do just as much to improve your experience of a place as a design that provides visual stimulation. Done well, you hardly notice acoustic panelling as it reduces cafeteria clamour to an atmospheric hum or makes airport call-outs more audible. A leading manufacturer in the sector is the Fantoni Group, which produces sound-deadening systems and a range of fit-out elements for the office. Managing director Paolo Fantoni introduces the company and its latest innovations.
Fantoni’s philosophy is to keep superior function in line with first-class design. Where did it all start?
Paolo Fantoni: As early as 1920 my grandfather came up with some important ideas about how to conduct the business. He wanted to have an art director involved in his small company – someone with a vision of how the market was developing and what tendencies were emerging. In those days that was quite an innovative attitude. He started advertising in Giò Ponti’s Domus and participating in fairs, which would later become the Salone del Mobile in Milan. In the 1950s and ’60s, when post-war industrialization came along, my father took responsibility for developing ideas. It was his relationship with architect Gino Valle that was fundamental to our activities at that time. Valle designed our new company buildings and the Fantoni campus in Osoppo, which is quite unique, thanks to a total vertical integration of production, from energy source to final product.
Offices, meeting rooms and workstations at the Fantoni showroom in Rome serve as real-life case studies for exhibiting the company’s products
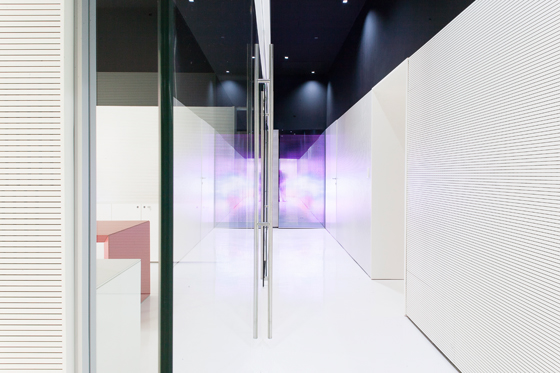
Offices, meeting rooms and workstations at the Fantoni showroom in Rome serve as real-life case studies for exhibiting the company’s products
×Part of that ‘total vertical integration’ means that Fantoni manufactures all materials and components for making the panels – from resin to impregnated papers and MDF.
Yes, Fantoni is actually a group of seven companies that carry out these activities, but that’s just a legal fact. In reality we are a unique group that’s been developed to form two core businesses. One is the production of panels and the other is furniture. But, yes, we make almost all the components we need ourselves.
What standards does an acoustic panel have to meet?
For 4akustik, we use a specific type of MDF with a very low formaldehyde emission level. It’s classified as an F4 Star level in accordance with JIS standards, which are based on a Japanese test for formaldehyde content that is even more stringent than the one used to set European standards. The panel is also Class 1 fire retardant. But the most important technical characteristic of the panel is, of course, its capability to absorb noise in common areas like cafeterias, restaurants, airports, theatres and so on.
The dining area of the European Space Agency in Rome has walls and ceilings panelled in Fantoni’s 4akustik system, which dampens sound to a minimum
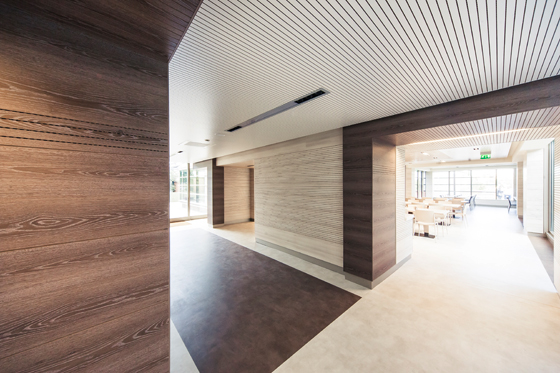
The dining area of the European Space Agency in Rome has walls and ceilings panelled in Fantoni’s 4akustik system, which dampens sound to a minimum
×How many projects feature Fantoni panels?
There is a huge list, but recently the Stock Exchange in Tel Aviv, Félix Candela’s L’Oceanogràfic marine park in Valencia, Málaga Airport, the cafeterias of Eni Group in Milan and Rome, Siemens in the UK, and a pavilion for the London 2012 Olympics.
Can the panels be customized?
Yes, we offer architects certain options that allow for personalized graphics. We can also rout the panels, using designs specified by the architect. We offer melamine-faced, lacquered and veneered finishes, but we also apply special HPL laminates upon request.
What’s the latest to come out of your research and development centre?
Right now we are working on a micro-perforated panel with holes that are almost invisible. The aim is a ‘real wood’ look that is different from the traditional acoustic panel with holes or strips. The new development should lead to an invisible way to make a sound-absorbing surface.
How do you ensure Fantoni’s panels are made sustainably?
The low formaldehyde content I mentioned is one aspect, but we also envision a reduced impact on the consumption of wood. Our chipboard is made with 100 per cent recycled wood, and our MDF panels and acoustic panels are totally recyclable, which is also important. In Southern Italy we have a factory that produces second-grade MDF, also made with 100 per cent recycled wood. At the moment, I know of no other place in Europe where this is being done.
Fantoni’s 4akustik sound-absorbent panel system was used in the restoration of Baluardo Della Cittadella in Modena, Italy
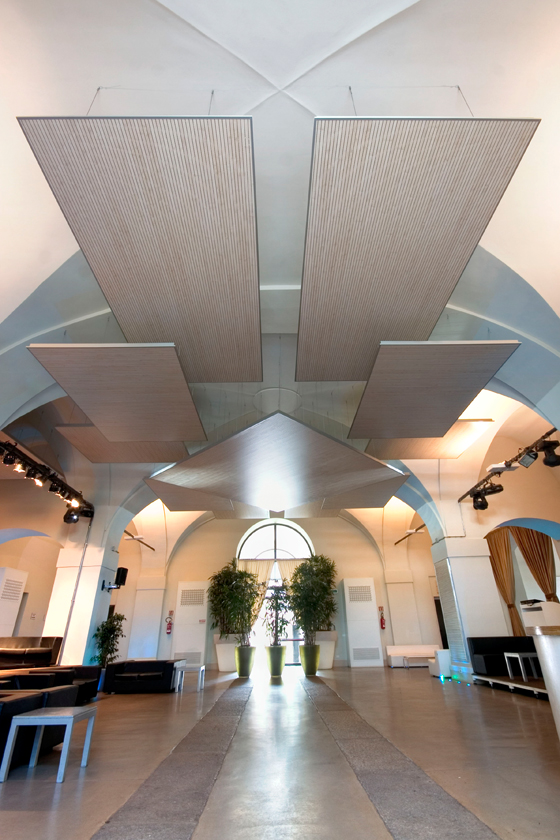
Fantoni’s 4akustik sound-absorbent panel system was used in the restoration of Baluardo Della Cittadella in Modena, Italy
×––
Fantoni
Location Osoppo
Established 1882
Number of employees 1100
Distribution 65 countries
Market sector Office furniture, partition and storage-wall systems, MDF and chipboard panels, melamine flooring, melamine papers and sound-deadening panels
Recognition Compasso d’Oro alla Carriera for Design Primario in 1998
Overall sales revenue €320 million
Website fantoni.it
––
Text: Riya Patel
Photos: Adriano Ferrara
––