A high-temperature laboratory for glass and light
Brand story by Ulrich Büttner
Berlin, Allemagne
02.03.15
The name of both the company and the brand is labo crème brûlée. It's a name which suggests fire and flames, and Christian Seltmann, his wife Tania Theler Seltmann and his brother Philipp are full of burning enthusiasm for their new project. The fourth generation of a porcelain-manufacturing family from Franconia ‘felt like doing something new’, which led to the establishment of their company in Majorca in the year 2009. However, since 2013 the firm has had its HQ and production facilities in Berlin. Here, they occupy a top location in a historic coach house between Mommsenstrasse and Kurfürstendamm, where there is also a showroom.
At labo crème brûlée, the ‘grand CRU’ pendant lamps are produced to customer-specific dimensions – because the requirements of space are always different
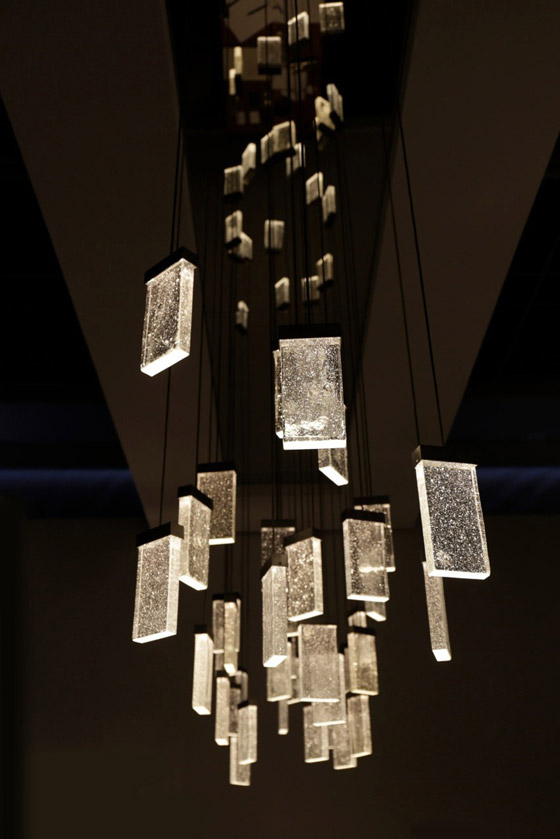
At labo crème brûlée, the ‘grand CRU’ pendant lamps are produced to customer-specific dimensions – because the requirements of space are always different
×In his teenage years, Christian Seltmann was already building furniture and lamps, and spent a lot of time in his own workshop. Tinkering, inventing, doing things with glass and light – this was his dream. He studied architecture and business administration, while his younger brother's subjects were materials engineering and ceramics. A heritage they both share is their expertise in terms of quality, reliability and design, combined with extensive know-how of furnace technology, melting operations and materials processing. Backed up by considerable interest in electronics, modern lighting technology as well as CAD and IT, the result was a manufacturing organisation creating products in which low-tech and high-tech come together in a fascinating and premium-quality way.
‘It was my vision and ambition to illuminate coloured glass. The breakthrough in LED technology around five years ago came exactly at the right time for us,’ recalls Christian Seltmann, adding: ‘My first LED lamp came from Ikea - with this ‘light baton’ I was able to do some basic research and see what happens when LEDs are combined with various types of molten glass.’ For a whole year the company's founder experimented with coloured glass, helped considerably by access to a prestigious glass foundry in Majorca.
Small-scale series such as the ‘grand Papillon’ wall lights represent the second mainstay of the labo crème brûlée collection
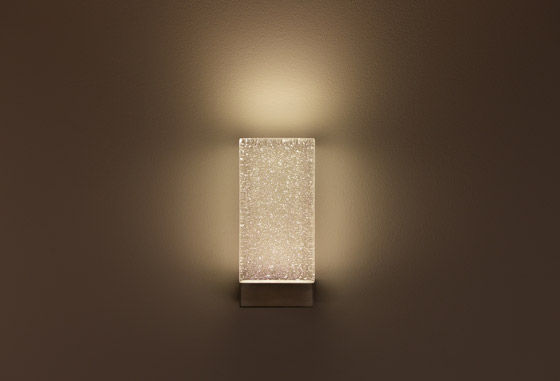
Small-scale series such as the ‘grand Papillon’ wall lights represent the second mainstay of the labo crème brûlée collection
×Labo crème brûlée is currently offering four products: the wall lights ‘pilote’ and ‘papillon’ (‘grand’ and ‘petit’) together with the pendant lamps ‘fleuve’ and ‘CRU’, with the latter also coming in ‘grand’ und ‘petit’ versions. ‘CRU’ is available as a round chandelier or ceiling canopy installation made up of pendant lamps, with customer-specific production of these large lighting objects representing the core expertise of the manufacturing company. ‘For the pendant lamps of our large ceiling-canopy installations or round chandeliers we use mainly white glass and - by virtue of the fact that every ceiling fixture is very specific - each of our products is virtually unique. We have never produced two identical chandeliers or installations, because the requirements relating to these objects are as different as the architecture in which they create their effect and as individual as our customers,’ emphasises Christian Seltmann.
A project which the company has recently completed is a ceiling installation with pendant lights in the boardroom of a Swiss pharmaceutical corporation. It is as if the installation highlights the very core of the company – the boardroom table. Labo crème brûlée was invited to create a large-scale installation with no less than 120 pendant lamps! The 7 x 1.5 m canopy had to be integrated into the existing air-conditioned ceiling as a high-tech object with sprinkler and beamer lift. Altogether the installation, for which none of the fixing materials are visible, weighs approximately half a tonne. These are the very challenges which the company's founders enjoy. The CAD-aided preparations are all made in Berlin and adapted to the blueprints of the architect. Painstaking advance planning and preliminary assembly then enable such lighting objects to be installed in only two days.
Part of an installation designed to customer-specific dimensions
A ‘grand CRU’ ceiling-canopy installation for a bar
With all the company's lamps, the light is diffused within the glass bodies. Because technical resources now enable the colour temperature to be set with great precision, LED technology is used exclusively in production. The LED modules can be selected in colour temperatures of 2580°, 2700° and 2780° Kelvin, with these fine differences of only 80° Kelvin visible in the glass. Only pure white LEDs are used because the colour is created by coloured glass. ‘Our five coloured glass types have a magical effect’ explains Christian Seltmann enthusiastically. ‘You couldn't achieve this with RGB and even if you did the colours wouldn't look right.’ The three colour temperature modules which are currently available cover a wide production range. In Asia, the taste is for cooler colours, while the Swiss would use candles wherever possible. Within each chandelier or installation, the glass pendants are all from the same melting process and LED qualities remain constant anyway, which accounts for the homogeneous nature of each lighting object.
In his capacity as head of R&D, Seltmann says confidently: ‘We are relatively advanced in terms of technical implementation and the relevant technology in the fields of LED and glass.’ The result is designs that achieve a decoratively appealing, almost scenographic picture, which supports the architectural aspects of its surroundings. And there can be no doubt that when a 240 cm x 50 cm canopy with 20 to 30 pendant lamps is suspended above a three-metre long dining table, this changes the entire appearance of the room.
The ‘petit Pilote’ wall light is flush-mounted and with a maximum installation depth of 52 mm it is also suitable for plasterboard walls
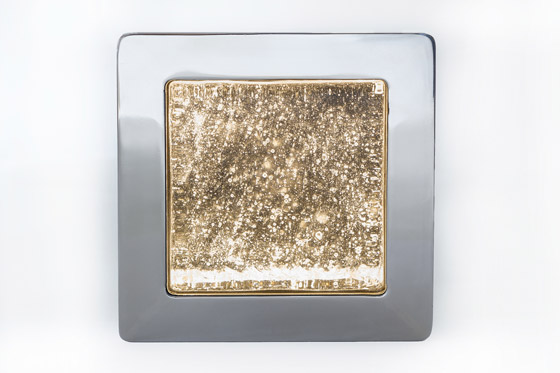
The ‘petit Pilote’ wall light is flush-mounted and with a maximum installation depth of 52 mm it is also suitable for plasterboard walls
×In spite of all the sophistication and complexity of the lighting technology, however, a central role is also played by the distinctive individual feature of the chandelier, its glass. It is the basic requirement for the special light that is radiated by the ‘CRU’ lighting objects, objects which are difficult to photograph, because the light radiated by the glass is absolutely free from glare. The glass shapes are poured by hand and enhanced by a pattern of bubbles. This pattern is different for each individual glass body or diffusor, which makes every single one unique. ‘We have carried out a lot of experiments and can now manage to create patterns of bubbles which are highly individual. Each glass body is like a miniature Milky Way,’ explains Christian Seltmann. The technology that is applied brings out the best in the glass while itself remaining concealed, with the visual effects created entirely within the glass body. The design motto at labo crème brûlée is one of maximum reduction, in line with the classical principle of “form follows function”. The lighting objects from Berlin are without any elements that are superfluous or simply decorative. This unadorned simplicity is in absolute contrast to the almost metaphysical lighting atmosphere and impact they create, which can only be generated by the individual glass.
The diffusors are made by hand and create an effect of being objets trouvés. They are delicate without being crystalline and harmonise especially well with rough materials or powerful design elements in their direct surroundings. The labo lamps have the impact of a brilliant solitaire diamond, but they don't radiate egocentricity. As a rule, there is nothing comparable in the room, which means that a ‘Grand GRU’ is always an object that creates an effect in itself and by itself, but without overpowering its surroundings, regardless of whether these themselves are Biedermeier or Bauhaus.
A ‘grand CRU’ chandelier with 45 pendant lamps lights the entrance to a castle in Bavaria
This is perhaps also the reason why labo products are in demand throughout the world's major cities. It is almost always interior designers, often in cooperation with a lighting planner, who recommend these premium-quality and highly individual chandeliers to their clients. However, without the latest communications technology it would hardly be possible to present these products throughout the world in a really impact-making way. Operating on a worldwide scale occasionally pushes the small team in Berlin to its very limits, but the overall elaborate production process involving individual, customised manufacture in itself imposes natural controls on the quantities which can be produced. The high demand therefore remains a constant challenge.
Exposure at Light+Building gave the young company a real boost, although the team are aware of the mystique of the new that is attached to them. They are also aware of the fact that they are at present the only ones capable of manufacturing products of this kind: ‘Tried-and-tested technology, spectacular beauty and functional perfection – with everything custom-made by hand in Germany,’ as Christian Seltmann puts it. Only the white LEDs are sourced from the market leader in Japan.