The Shapeshifter: material innovation FluidSolids
Brand story by Simon Keane-Cowell
Zürich, Suisse
16.10.13
Nominated for this year's Design Prize Switzerland, Zurich-based designer Beat Karrer's material innovation FluidSolids, with its strong ecological credentials and impressive programmability, is poised to give traditional materials like metal and plastic a run for their money. The future is fluid.
_
Swiss designer Beat Karrer's 'FS Stool', which puts his innovative FluidSolids material to the test, was awarded a 2011 Materialica Design + Technology Award in the CO2 Efficiency category
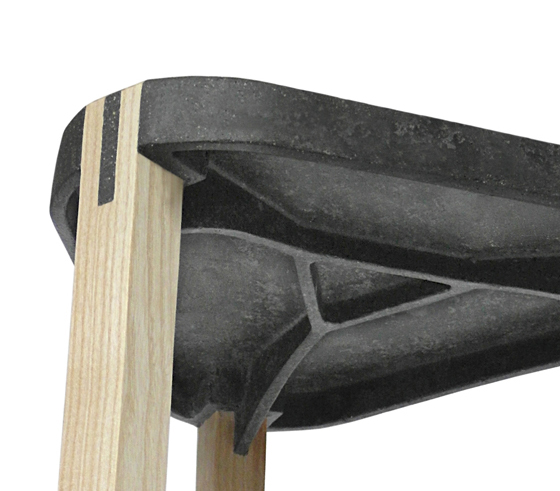
Swiss designer Beat Karrer's 'FS Stool', which puts his innovative FluidSolids material to the test, was awarded a 2011 Materialica Design + Technology Award in the CO2 Efficiency category
×Every now and then a design innovation comes along that has the potential to be a complete game-changer. One of the nominations for the 2013 Design Prize Switzerland – a long-established and well-respected accolade in a country where good design is part of the DNA of everyday life – is such an innovation.
The brainchild of Zurich-based product designer Beat Karrer (or ‘product thinker’ as he elects to describe himself, thereby underscoring the problem-solving smarts he brings to bear on his work), FluidSolids is an entirely new, paradigm-shifting material. Beyond its impressive ecological credentials – it’s made entirely of industrial by-products and is fully biodegradable – it offers, as its name would suggest, enormous flexibility in production and application terms. The wonder stuff, which consists of fibre, a filling material and a binding agent, can be moulded and extruded into highly precise structural components and products that, both lightweight and durable, replace the need for metal or plastic. ‘As a designer,’ says Karrer, ‘the idea of having a material that can be adapted with regard to strengths and physical properties, colours and appearance – it’s kind of a dream.’ This is a design development with the ability to change how we design.
Flexibility is the watchword of FluidSolids – beyond the material's impressive ecological credentials, a range of colours and surfaces is possible
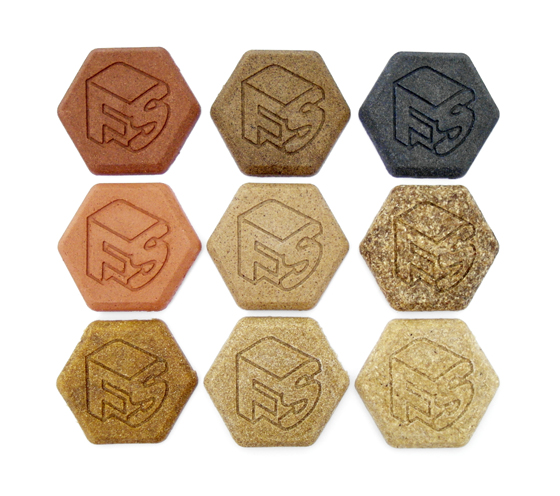
Flexibility is the watchword of FluidSolids – beyond the material's impressive ecological credentials, a range of colours and surfaces is possible
×The story of FluidSolids’ development is as fluid as the material itself. A workshop at the Vitra Design Museum in 2008 functioned as catalyst for the project. Here, while experimenting with ‘homemade’ bioplastics made of, among other things, starch from peeled potatoes, Karrer got to know fellow-participant Michael Kangas, a biochemist. Their meeting would see them collaborate for the next year and a half on a number of what the designer calls ‘recipes’ – material compositions derived from cheap and affordable waste products that, when combined, add value to design by providing a wealth of new physical and formal possibilities. ‘I believe that – apart from social influences – materials and production technologies are the driving forces in design,’ explains Karrer. ‘My studio isn’t particularly interested in shaping or styling, but in materials. If you have a new material, what can you do with it? How can you get added value out of it?’
Experimentation is the name of the game at Beat Karrer's Zurich studio. 'If you have a new material,' asks Karrer, 'what can you do with it? How can you get added value out of it?’
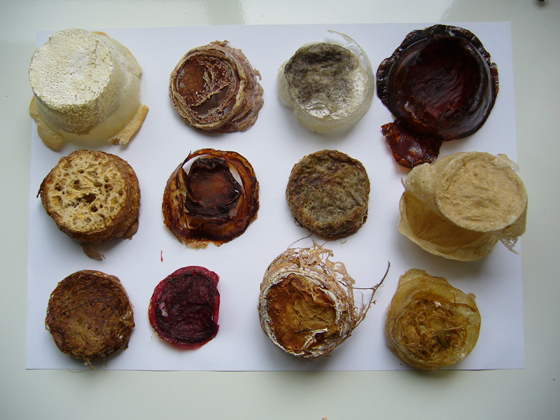
Experimentation is the name of the game at Beat Karrer's Zurich studio. 'If you have a new material,' asks Karrer, 'what can you do with it? How can you get added value out of it?’
×At the heart of the FluidSolids project lies an entrepreneurial drive and a commitment to experimentation. After Kangas quit the team, Karrer kept going, changing the composition and identifying a new binder. To say that the process was an iterative one would be an understatement. A total of ten basic recipes were explored, with Karrer creating for each over 50 different samples, every one finely calibrated in terms of additives. ‘Several things we found out were not completely expected,’ says Karrer. ‘And others were confirmed by experimenting. You have to negotiate what doesn’t work while holding onto what does work. Then it’s a case of carefully adjusting the additives, as you are already quite close. The last ten percent of the recipe is the most difficult.’
The experimentation-driven process of developing FluidSolids saw Karrer and his team create over 500 samples
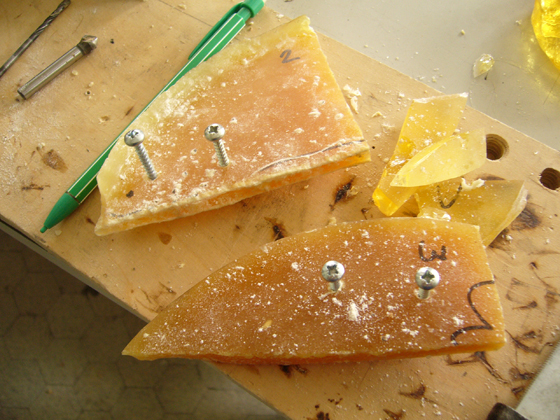
The experimentation-driven process of developing FluidSolids saw Karrer and his team create over 500 samples
×Once FluidSolids’ final composition had been determined, it was time to bring the new biopolymer material to life by applying it. With financial resources in place, the team established, and the production technology up and running, Karrer designed a bowl and a stool in FluidSolids, which acted, manifesto-like, as vehicles for demonstrating the range of colours and surfaces possible, and its precision-moulding properties, respectively. So convincing is the stool’s construction – thanks to the use of FluidSolids, the legs elements can be bonded directly with the material during the moulding process, dispensing with the need for glue, screws or any other kind of joint technology – it picked up a Materialica Design + Technology Award in 2011 in the CO2 Efficiency category.
Putting FluidSolids' properties through their paces: the new biopolymer material being extruded (top) and undergoing a tensile test (above)
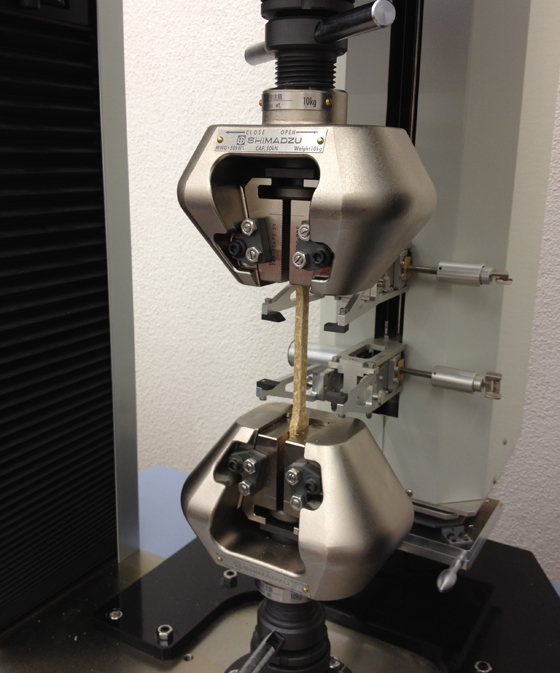
Putting FluidSolids' properties through their paces: the new biopolymer material being extruded (top) and undergoing a tensile test (above)
×What such a plaudit actually acknowledges, however, is something quite fundamental in terms of material programmability. Karrer explains: ‘As designers, we’re always interested in materials that suit our design vision or concept, rather than adapting a design to a given material. Most of the time, you’re working with semi-fabricated materials and often it gets to the stage where you have to redesign or adapt your design to the material.’ FluidSolids, which requires very little energy to produce and process, and is, moreover, completely non-toxic and compostable, allows designs to take shape exactly how they are envisaged, without compromise.
Karrer's award-winning 'FS Stool', whose wooden legs are inserted into the Fluid Solids seat during moulding, dispensing with the need for glue and screws, and his 'FS bowl', which is akin to wood in terms of touch, but possesses the fluid form of plastic
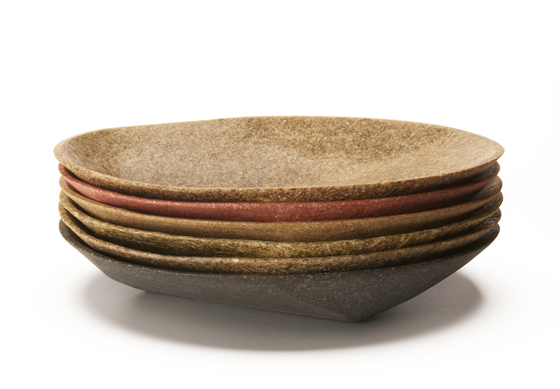
Karrer's award-winning 'FS Stool', whose wooden legs are inserted into the Fluid Solids seat during moulding, dispensing with the need for glue and screws, and his 'FS bowl', which is akin to wood in terms of touch, but possesses the fluid form of plastic
×2012 saw FluidSolids take to the stage, when it made its first public appearance at the Milan Furniture Fair in the form of Architonic’s Concept Space IV. Here, the material was moulded into a uniform, repeated element, which, when interconnected, created a highly architectural presence that garnered significant interest from fair-goers. Subsequent installations of the concept space at various trade fairs internationally, each iteration in Architonic’s key brand colour anthracite, have presented different configurations of the same elements, responding to the specific stand spaces in which they are put to work. Such system flexibility functions on a metaphorical level, too, speaking as it does of the superlative flexibility of the material itself.
FluidSolids serves to create architectural space in the form of Architonic's Concept Space IV (top), and moulding one of the uniform, repeated elements for the project (above)
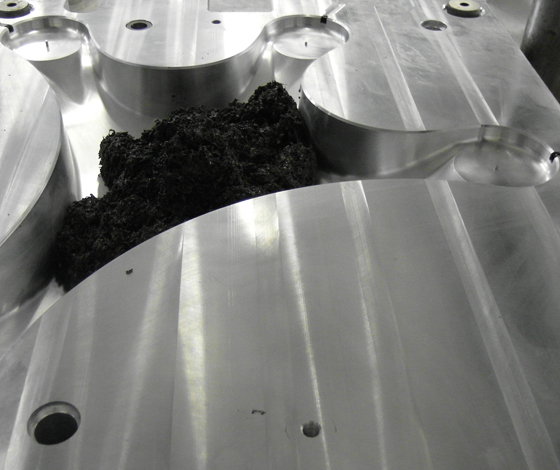
FluidSolids serves to create architectural space in the form of Architonic's Concept Space IV (top), and moulding one of the uniform, repeated elements for the project (above)
×With a number of patents for FluidSolids under his belt, which allow his company to manufacture products in the cutting-edge material and to sell the material itself, Karrer is looking to the future. A project with a partner in China is already underway, which will see the roll-out of a new generation of retail mannequins, ones that dispense with the need for polyester and fibre-glass in their fabrication. Production is starting in Switzerland, with plans to build a second, scaled-up plant in China. Parallel to this, Karrer is working on a new production technique for FluidSolids, one that will permit manufacturing on an even more industrialised basis, ideal for large series.
So, whoever scoops this year’s Design Prize Switzerland, one thing is certain: while FluidSolids may be super flexible, it’s quickly becoming a firm fixture in the materials landscape.
Here, there and everywhere: FluidSolids is exhibited at part of Skopje Design Week (top), and Beat Karrer with his wonder material in his Zurich studio (above)
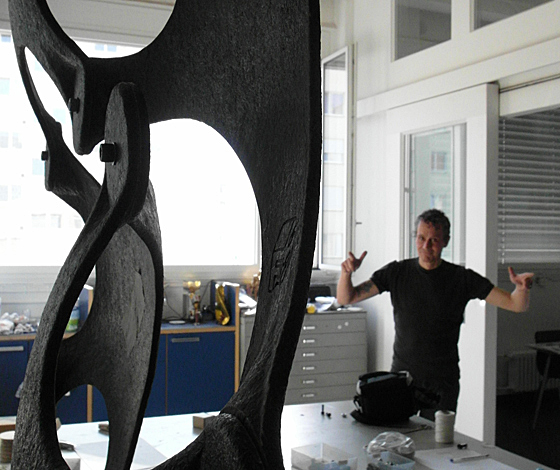
Here, there and everywhere: FluidSolids is exhibited at part of Skopje Design Week (top), and Beat Karrer with his wonder material in his Zurich studio (above)
×...