The Very Fabric of Architecture: textile use in construction
Texte par Susanne Fritz
Suisse
20.08.11
Most people have at one time or another spent the night in a tent and have benefited from the protection provided by its fabric, while at the same time enjoying the sensation of being separated from nature by nothing more than a thin shell. Textile forms of habitation have a long history going back to palaeolithic times and represent an archetypal form of building which has endured to the present day. Textiles are light, easy to convert or dismantle, and they provide protection against wind, ultra-violet rays and rain.
Tahari Showroom, New York; Photo © Gisela Stromeyer
Modern architecture has rediscovered the principle of the tent as an architectural form and taken its development further – not just for temporary structures but also for permanent buildings. Advanced and durable fabrics enable large areas to be spanned, which has turned their use into a highly specialised sector within the construction industry. At the same time the specific static demands made on textiles by wind load, weathering and distortion together with structural factors such as mounting and bracing these textile elements require a great deal of engineering know-how.
Producing stretches of fabric and cutting them to size is implemented on the basis of complex patterns which, thanks to the latest computer technology, can also integrate statically relevant factors.
In this article and those that will follow in our series on 'The Fabric of Building: Textile Architecture' we will be describing textile structures used in a wide range of architectural applications and highlighting the diversity of fabrics employed in architecture.
Tahari Showroom, New York; Photo © Gisela Stromeyer
Cloth is the material from which the Elie Tahari fashion company designs exclusive creations - and cloth is also the design element with which Gisela Strohmeyer has converted an uninspiring room without any daylight into an elegant showroom.
For the presentation of the collection and for cupboards large, semi-oval openings were cut into the swatches of material. A column at the centre of the almost square room supports two different types of fabric, one of them transparent and the other opaque. The backlit sections of cloth are not sewn together but connected by a large number of hooks. As a result the swatches of cloth are only attached to each other at specific points, which visually highlights the elasticity of Lycra as a material and has the positive aspect that the sections of cloth can be taken apart again. The installation is also fastened to the walls and ceiling by hooks, while on the floor it is held in place by movable weights. When the textile elements are no longer required they can be folded up and stored compactly in a cupboard. In addition the fabrics are machine washable.
Textile installation at the Whitney Museum of American Art; Photo © Gisela Stromeyer
The DAR LUZ project by Lars Meeß-Olsohn and Ali Heshmati was one of the installations at a recent light art walkway in Eindhoven, where the textile skin operated as a projection screen for staging a dynamically controlled light show. A number of sensors detected the movements of visitors and transmitted these to the LED spotlights which responded with individually changing colour sequences and intensity of lighting effects.
DAR LUZ installation by Lars Meeß-Olsohn and Ali Heshmati in Eindhoven; Photo © Johan Creemers
The temporary installation was constructed using standard roof battens screwed together into 22 square frames and attached to the wooden walkway at an angle of 15° to one another. A hundred and fifty square metres of elastic, impregnated fabric was then stretched over this ingenious wooden structure.
DAR LUZ installation by Lars Meeß-Olsohn and Ali Heshmati in Eindhoven; Photo © Patrik Matheeuwsen
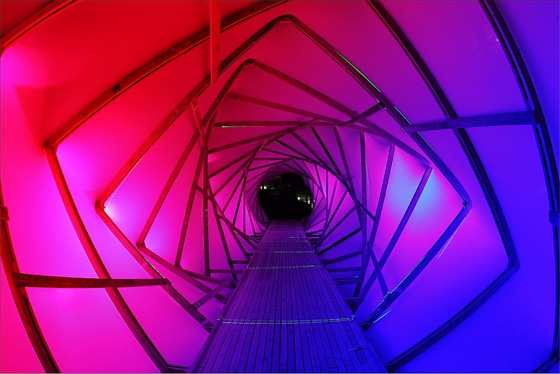
DAR LUZ installation by Lars Meeß-Olsohn and Ali Heshmati in Eindhoven; Photo © Patrik Matheeuwsen
×'Tubaloon' is the name given by the architects Snohetta to the 20 m x 40 m pneumatic membrane sculpture which was created for the Kongsberg jazz festival in Norway. The combination of a stretched membrane with a pneumatic design is the special feature of the Tubaloon: stretched membrane structures have exterior structural parts but in the case of the Tubaloon the static structure is located like a skeleton inside the pneumatic shell. This gives the structure a body-like, organic look. Every year the Tubaloon is set up and dismantled once more and so a white, PVC-coated PVC-PES polyester membrane by Ferrari was selected because of its hardwearing properties and its suitability for projection and acoustic purposes.
'Tubaloon' textile sculpture by Snohetta for the Kongsberg Jazz Festival; Photo © Snohetta
'Tubaloon' textile sculpture by Snohetta for the Kongsberg Jazz Festival; Photo © Snohetta
The resistance to weathering shown by membranes made of PVC-coated polyester is also demonstrated by the Venezuelan pavilion constructed at Expo 2000 in Hanover. The structure, which was designed by the Venezuelan architect Fruto Vivas, was dismantled after the fair and shipped to Venezuela in over 50 containers. It took six years to find a new location for it there and during that time the membranes were stored in their steel containers in the heat of Venezuela, having to withstand temperatures of over 80°C. In spite of this all the original membranes were suitable for re-use.
Venezuelan pavilion designed by architect Fruto Vivas; construction: Rasch und Bradatsch Architekten / 3dtex GmbH
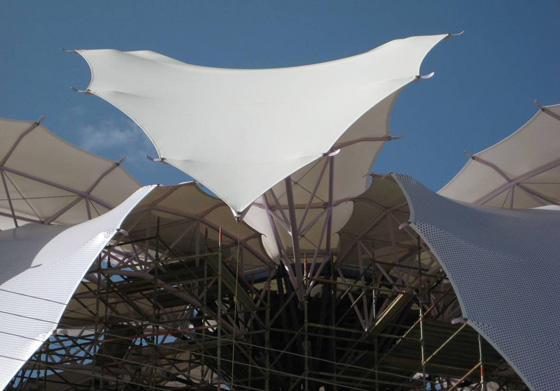
Venezuelan pavilion designed by architect Fruto Vivas; construction: Rasch und Bradatsch Architekten / 3dtex GmbH
×A protective film gives the surface of PVC-PES membranes anti-adhesive properties, which means that the material remains dirt-resistant for years and is easy to clean. Depending on the climatic conditions, individual application and the demands made on them they can last up to twenty years.
Thanks to its tensile strength and special flexibility PVC-PES can be universally applied, and is used in particular for roof and facade applications. Its special features are its relatively high level of transparency, low-flammability fire classification and resistance to creasing.
Venezuelan pavilion designed by architect Fruto Vivas; construction: Rasch und Bradatsch Architekten / 3dtex GmbH
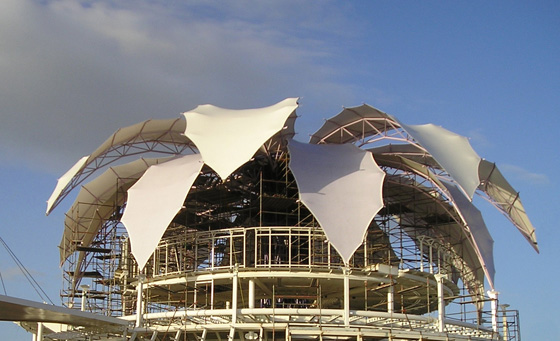
Venezuelan pavilion designed by architect Fruto Vivas; construction: Rasch und Bradatsch Architekten / 3dtex GmbH
×The facade of a company building in Vienna has been fitted with a total of 104 sails which on the one hand protect the building from the sun and on the other act as architectural cladding on the closed side of the building. The vertical sails were produced in hypar shape from the Soltis 86 material made by Ferrari, also PVC-coated polyester.
The firm of Planex calculated the dimensions of each sail by modelling based on highly accurate measurements, and all the seams were welded using high-frequency welding equipment.
The Soltis material is produced using precontraint technology. During manufacturing both the warp and the weft yarn is pre-stressed and then coated. This guarantees a high level of surface stability and is a precondition for ensuring adequate wind resistance, which can only be guaranteed if the sails neither expand nor contract in response to changes in temperature. Soltis is UV-resistant and is available not just with perforations of varying sizes and the corresponding variable transmittance but also in a range of different colours.
The Soltis material by Ferrari is produced using precontraint technology: during manufacturing both the warp and the weft yarn is pre-stressed and then coated
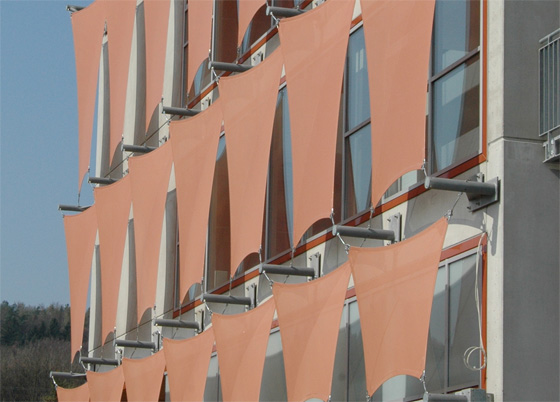
The Soltis material by Ferrari is produced using precontraint technology: during manufacturing both the warp and the weft yarn is pre-stressed and then coated
×A textile facade in the extended sense covered the Swiss pavilion at the 2010 Shanghai EXPO – a steel net made of galvanised wire strands with a diameter of four millimetres made by the firm of Carl Stahl formed the 3,800 m2 and 15 m high facade, which was fitted with 11,000 cells made of sustainable polycarbonate that generated electricity by means of solar technology.
The same steel netting by the name of X-TEND was also used for covering the aviary of the Loro Parque in Tenerife. The rolls of steel netting can be manufactured to any required length and the individual sections can also be joined crosswise to an unlimited extent without detracting from the strength of the netting.
Swiss pavilion at EXPO Shanghai 2010 with X-TEND Edelstahl-Seilnetz by Carl Stahl Architektur; Photo © iart interactive ag, photographer: Mark Niederman
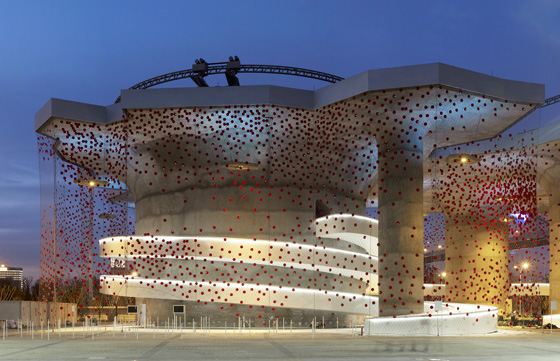
Swiss pavilion at EXPO Shanghai 2010 with X-TEND Edelstahl-Seilnetz by Carl Stahl Architektur; Photo © iart interactive ag, photographer: Mark Niederman
×Swiss pavilion at EXPO Shanghai 2010 with X-TEND Edelstahl-Seilnetz by Carl Stahl Architektur; Photo © iart interactive ag, photographer: Mark Niedermann
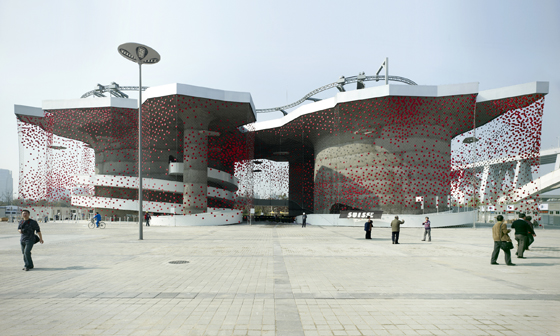
Swiss pavilion at EXPO Shanghai 2010 with X-TEND Edelstahl-Seilnetz by Carl Stahl Architektur; Photo © iart interactive ag, photographer: Mark Niedermann
×The importance of this feature becomes clear in the light of the dimensions of the open-air aviary, which has a volume of 17,000 cubic metres. The netting has an area of 3,200 square metres and weighs 31 tonnes. The highest point of the structure is 32 metres. A bridge enables a number of views from different perspectives of the aviary with its more than one hundred species of Australian and Asian birds.
The fact that the filigree netting is hardly noticeable is the result of a special process in which the entire structure of the net (all strands and clips) is coloured black and accordingly disappears against the vegetation of the jungle landscape.
Loro Parque open-air aviary on Tenerife: the fact that the filigree netting is hardly noticeable is the result of a special process in which the entire structure of the net is coloured black. Photo: ©Kissner
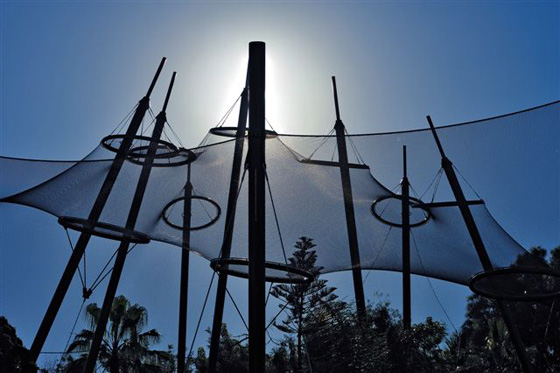
Loro Parque open-air aviary on Tenerife: the fact that the filigree netting is hardly noticeable is the result of a special process in which the entire structure of the net is coloured black. Photo: ©Kissner
×For the Architonic Concept Space at imm cologne 2008 it wasn't a sub-tropical but an arctic landscape which was created. The architects Lava designed umbrellas on which drifting ice floes were projected. The amorphous aluminium umbrellas were covered with a transparent membrane which was cut to size using CNC technology in cooperation with the Australian firm of Global Membrane Designs.
Architonic Concept Space at imm cologne 2008 by l-a-v-a architects
Architonic Concept Space at imm cologne 2008 by l-a-v-a architects
Whereas the above examples present fabrics stretched over a sub-structure, the shape and design of the exterior curtain of House 47°40’48”n/13°8’12”e are exposed to the forces of the wind.
For the black curtain the architects Maria Flöckner and Hermann Schnöll used industrial netting which is also usually applied as wind shielding or for covering crops.
The material derives its stylish appearance from the clever choice of transparency and gloss, as well as its ruffled mounting. It enables the transparent facade to be regulated and removes the need for classical sun and sight screening for the building's full-length windows. As it shifts in the breeze the curtain enhances this modern and unadorned building with an opulent and theatrical touch.
Exterior curtain at House 47°40’48”n/13°8’12”e: the architects Maria Flöckner and Hermann Schnöll used industrial netting; Photo © Stefan Zenzmaier, zenz@sbg.at
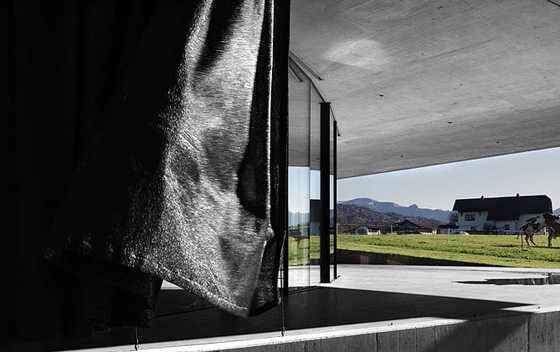
Exterior curtain at House 47°40’48”n/13°8’12”e: the architects Maria Flöckner and Hermann Schnöll used industrial netting; Photo © Stefan Zenzmaier, zenz@sbg.at
×House 47°40’48”n/13°8’12”e by Maria Flöckner and Hermann Schnöll; Photo © Stefan Zenzmaier, zenz@sbg.at
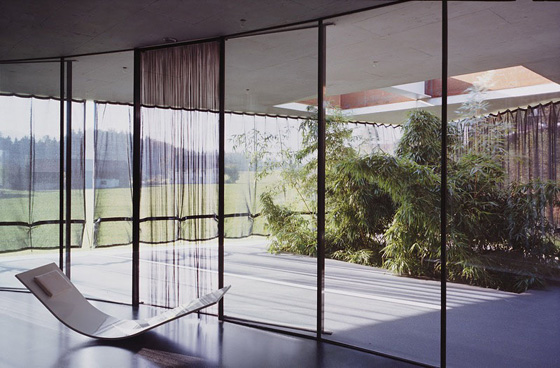
House 47°40’48”n/13°8’12”e by Maria Flöckner and Hermann Schnöll; Photo © Stefan Zenzmaier, zenz@sbg.at
×House 47°40’48”n/13°8’12”e by Maria Flöckner and Hermann Schnöll; Photo © Stefan Zenzmaier, zenz@sbg.at
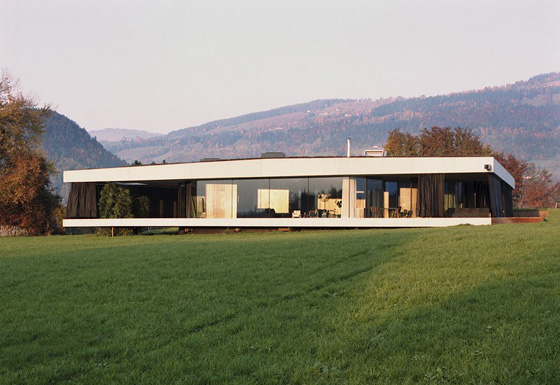
House 47°40’48”n/13°8’12”e by Maria Flöckner and Hermann Schnöll; Photo © Stefan Zenzmaier, zenz@sbg.at
×Whether it's the innovative use of industrial netting as in the last example or the use of special architectural membranes – the potential for the use of fabrics in construction design is far from exhausted because many high-tech textiles used in industry are not yet available for building applications.
At the same time building with textiles and above all the use of membranes are becoming increasingly important in architecture and are being applied to an ever-greater extent in major projects, a subject which will be looked at in the next article in our 'Textile Architecture' series.
© Architonic
Head to the Architonic Magazine for more insights on the latest products, trends and practices in architecture and design.