The Printed Environment: 3D printing goes architectural
Scritto da Alyn Griffiths
London, Regno Unito
12.09.13
3D-printed architecture might seem like the stuff of the future, but a number of architects are experimenting to try to turn tomorrow's fantasy builds into today's innovative projects. Architonic investigates.
Over the past decade, additive manufacturing, or 3D printing as it is more commonly known, has been gradually making the transition from a tool used by the creative industries to produce fast prototypes for testing, to a viable method of manufacturing retail-ready products.
However, the machinery and materials remain expensive, and so the huge potential of 3D printing is still underdeveloped. On an architectural scale, the costs become even more prohibitive, but this isn’t stopping some architects from attempting the near-impossible of imagining what the future might bring. Customised buildings that can be printed on site, surfaces that combine strength and decoration through digitally optimised designs, and sustainable structures printed from natural materials are some of the revolutionary possibilities being explored by pioneers of large-scale printed structures.
Structure printed by Enrico Dini’s D-Shape machine being extracted from the loose sand
So far, applications for 3D printing in architecture have been restricted to prototypal scale models and a couple of full-scale follies that demonstrate how the process could be used, in principle, to produce habitable structures. Italian entrepreneur Enrico Dini was the first to print a structure on an architectural scale, using his enormous D-Shape printer. This machine comprises a giant rig that lays down layers of sand, onto which a row of nozzles linked to CAD software deposits a binding agent that solidifies the sand and transforms it into a type of artificial sandstone.
The D-Shape printer in action. Dark areas show where a layer of the chlorine-based binder has just been deposited
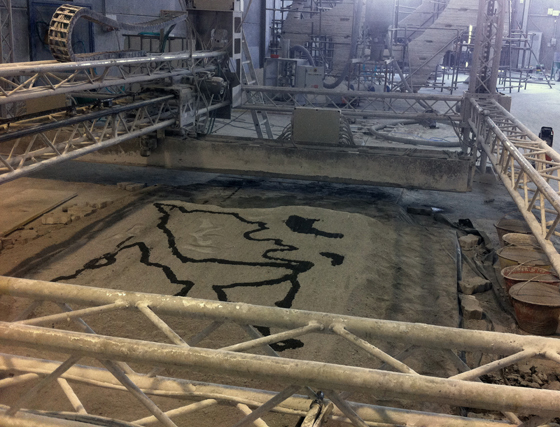
The D-Shape printer in action. Dark areas show where a layer of the chlorine-based binder has just been deposited
×Dini’s experiments, including the manufacture of a 3-cubic-metre, self-supporting pavilion, designed in 2009 by Italian architect Andrea Morgante, demonstrated the potential of printing full-scale but also encapsulated some of the problems. “The material is very fragile and last year when we tried to deliver a two-and-a-half tonne sculpture to a gallery in New York, we underestimated the amount of packing material and it broke,” recalls Dini. “The other issues with the machine right now are that the feeding system for the printer is not reliable and the process of evacuating the sand is very laborious and very dusty.” He adds that, despite being conceptually very simple, these elements are extremely expensive. “Currently, our main problems are all about funding, not technical things.”
Enrico Dini recognises that the problems he has encountered with his giant printer will eventually be overcome, if not by him then by his competitors. He says that his work has captured the imagination, “first of designers, then of architects, then of constructors and now of private investors and venture capitalists who see that it is possible to manufacture digitally with this deposition process in full scale.”
Landscape House by Universe Architects could be printed in one continuous section
Indeed, architects are already proposing ambitious buildings based on the capabilities of the D-Shape printer. The Landscape House designed by Janjaap Ruijssenaars of Dutch firm Universe Architecture, for example, takes the form of an endless Möbius strip that the architect believes could be printed in one piece without having to rely on extremely complex moulds. External and internal surfaces, including staircases, would be printed at the same time and would retain the raw, pixellated finish that results from tolerances built into the deposition process. Ruijssenaars believes that printing in this way would save time, labour and energy, and enable the construction of a wall-less structure that would become part of the surrounding landscape.
Moon base designed by Foster + Partners to be printed from lunar soil. Image © Foster + Partners
The way in which the D-Shape printer transforms loose particles of sand into a solid structure has a magical, science-fiction appeal, so perhaps it is little wonder that it is being examined by some of the world’s leading space agencies with a view to constructing dwellings elsewhere in the solar system.
The modular system comprises interconnected inflatable domes covered in a printed shell. Image © Foster + Partners
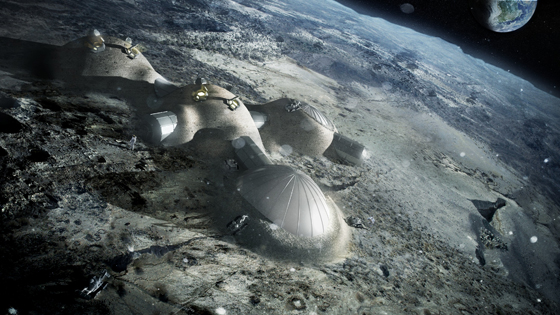
The modular system comprises interconnected inflatable domes covered in a printed shell. Image © Foster + Partners
×Robots combine the soil with a binding agent and 3D print a lightweight but robust cellular structure. Image © Foster + Partners
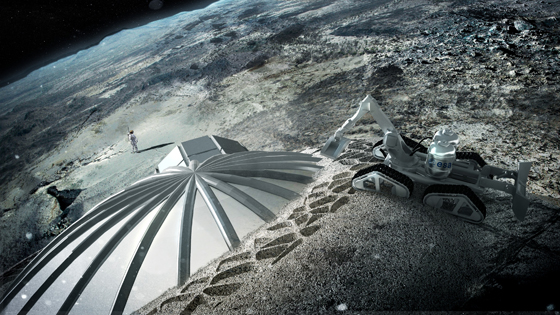
Robots combine the soil with a binding agent and 3D print a lightweight but robust cellular structure. Image © Foster + Partners
×The European Space Agency has collaborated with London architects Foster + Partners to develop a proposal for a 3D-printed moon base built from lunar soil, known as regolith. The structures would be formed around an inflated dome, onto which layers of regolith combined with a binding material would be deposited by a robotically operated printer. Printing a specially developed cellular structure similar to foam would reduce the density of the structure and the amount of binding material required, while producing a shell strong enough to protect its inhabitants from the moon’s inhospitable atmospheric conditions. Such a seemingly far-fetched proposition could easily be dismissed as sci-fi fantasy, but the team has already conducted trials in a vacuum chamber using simulated lunar soil.
Proposed design for the 3D-printed Canal House by DUS, showing a facade that will become more detailed towards the top as the printing technique is optimised over time
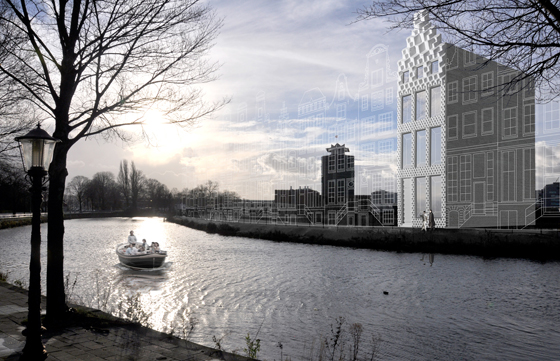
Proposed design for the 3D-printed Canal House by DUS, showing a facade that will become more detailed towards the top as the printing technique is optimised over time
×A 1:20 scale model of the Canal House site, showing the position of the KamerMaker inside its shiny metal pavilion
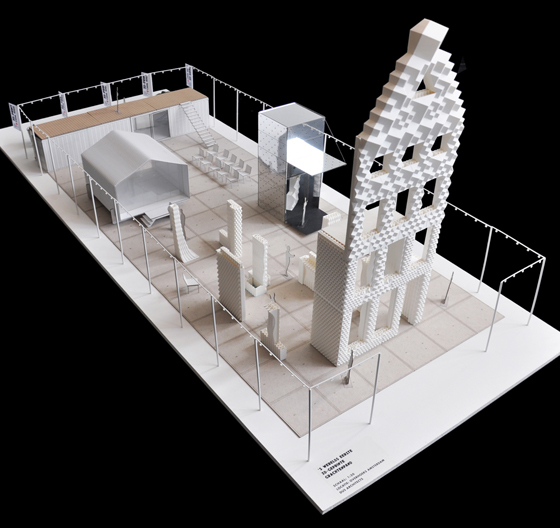
A 1:20 scale model of the Canal House site, showing the position of the KamerMaker inside its shiny metal pavilion
×Back on Earth, the alternative to printing entire structures on an enormous machine is to print smaller sections that can combine to produce a full-scale building. This is the approach adopted by Dutch architecture studio DUS, which has begun printing test blocks for a canal house it plans to construct in Amsterdam using an upsized version of a desktop Ultimaker printer called the KamerMaker (Room Maker). Parts for the building will be printed on site inside the six-metre-high KamerMaker and assembled gradually, in view of the public to create a contemporary version of a traditional four-storey canal house. The project is intended as an accessible research and development exercise, with the design expected to change as the team learns the strengths and weaknesses of the materials and equipment. “Our goal is to have it completely printed but I can imagine that we are still going to use some other materials,” explains Martine de Wit, a founding partner at DUS. “It’s also very interesting to see how the combination of more traditional building materials, such as glass, will work alongside the 3D printed parts.”
A full-scale rosette window frame. Every window and building component will be unique
The building will also act as a tool for promoting 3D printing, as the site is open to the public, with regular talks and workshops explaining the process to interested parties and potential partners. The first target for DUS is to construct a two-storey “welcoming room” that will provide a showcase for the project’s progress, and it also plans to print and erect the full facade as a monument to attract passers by. De Wit says that the response so far has been extremely positive, with many people turning up to watch the printer in action. Inevitably, however, the project also has its sceptics. “There are people who say it's never going to happen, that it’s all just hype, while others say it's definitely going to change the way we make things,” de Wit points out.
Softkill Design’s ProtoHouse is based on the fibrous structure of bones, which only grow material where it is needed. Photo by Julia Kubisty
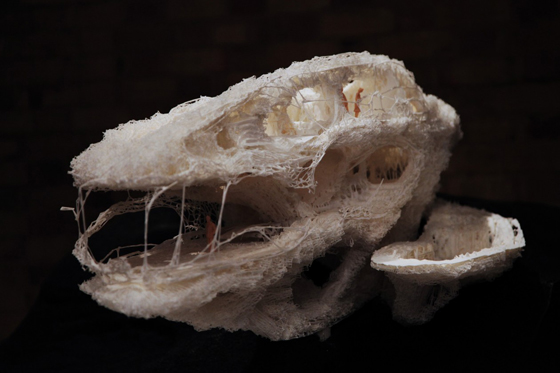
Softkill Design’s ProtoHouse is based on the fibrous structure of bones, which only grow material where it is needed. Photo by Julia Kubisty
×On a more conceptual level, some architects are attempting to identify the real disruptive potential of 3D printing, and how it could provoke entirely new building typologies. During their studies at the Architectural Association, Nicholette Chan, Gilles Retsin, Aaron Silver and Sophia Tang of London architecture studio Softkill Design developed a proposal for a 3D printed home with a fibrous shell inspired by the way bones grow. Using a custom-designed algorithm, the team was able to optimise the structure so that material is only deposited where needed.
The structure would be built from 31 pieces printed individually and assembled on site
The graduates propose that the house be printed in 31 individual sections that fit the capacity of machines that are currently available. The pieces would then be trucked to site and locked together without the need for any additional fixings, with a waterproof membrane suspended inside the web-like frame to provide shelter. The 1:33 scale model produced by Softkill Design provides a compelling vision of how 3D printing can combine with the latest parametric software to produce forms that would be impossible to create using conventional construction methods.
A completed work from Enrico Dini’s D-Shape printer that demonstrates the sort of organic shapes enabled by 3D printing
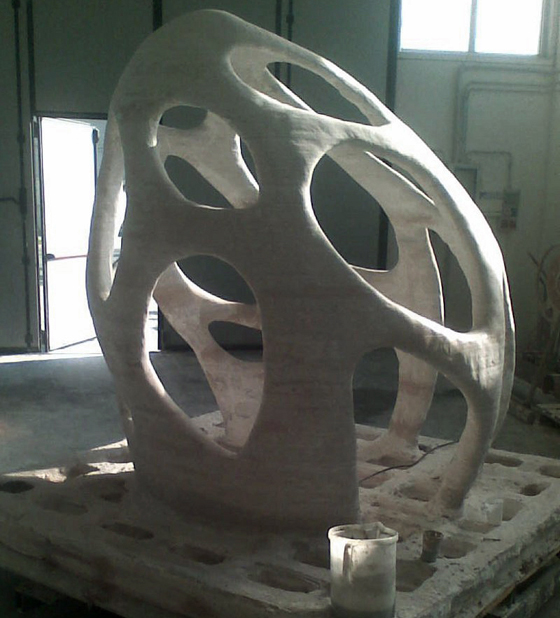
A completed work from Enrico Dini’s D-Shape printer that demonstrates the sort of organic shapes enabled by 3D printing
×It’s impossible to predict whether we’ll all one day be living in a web of delicate dwellings printed by robots, or indeed in regolith caves on the moon. It is, however, inevitable that 3D printing technology will continue to evolve, and as the cost and complexity decreases, architects will be encouraged to explore its potential to build in ways that are more sustainable, economical and efficient. Martine de Wit believes the revolution has already begun: “In five years I think it will be quite normal to use 3D printing in the building industry, and looking even further [ahead] maybe half of everything we build will be 3D-printed.”