Lockdown lighting: Joe Scog
Storia del Marchio di Emma Moore
London, Regno Unito
16.03.21
With a pandemic and quarantine to contend with, British lighting brand Joe Scog’s ethos of utilising existing components, handmade elements and waste materials wherever possible was again put to the test in the creation of its latest luminaire...
The Lockdown Task Lamp, Joe Scog’s new desk light, was conceived and engineered during the UK’s first lockdown using parts that were available locally or that could be produced easily by hand
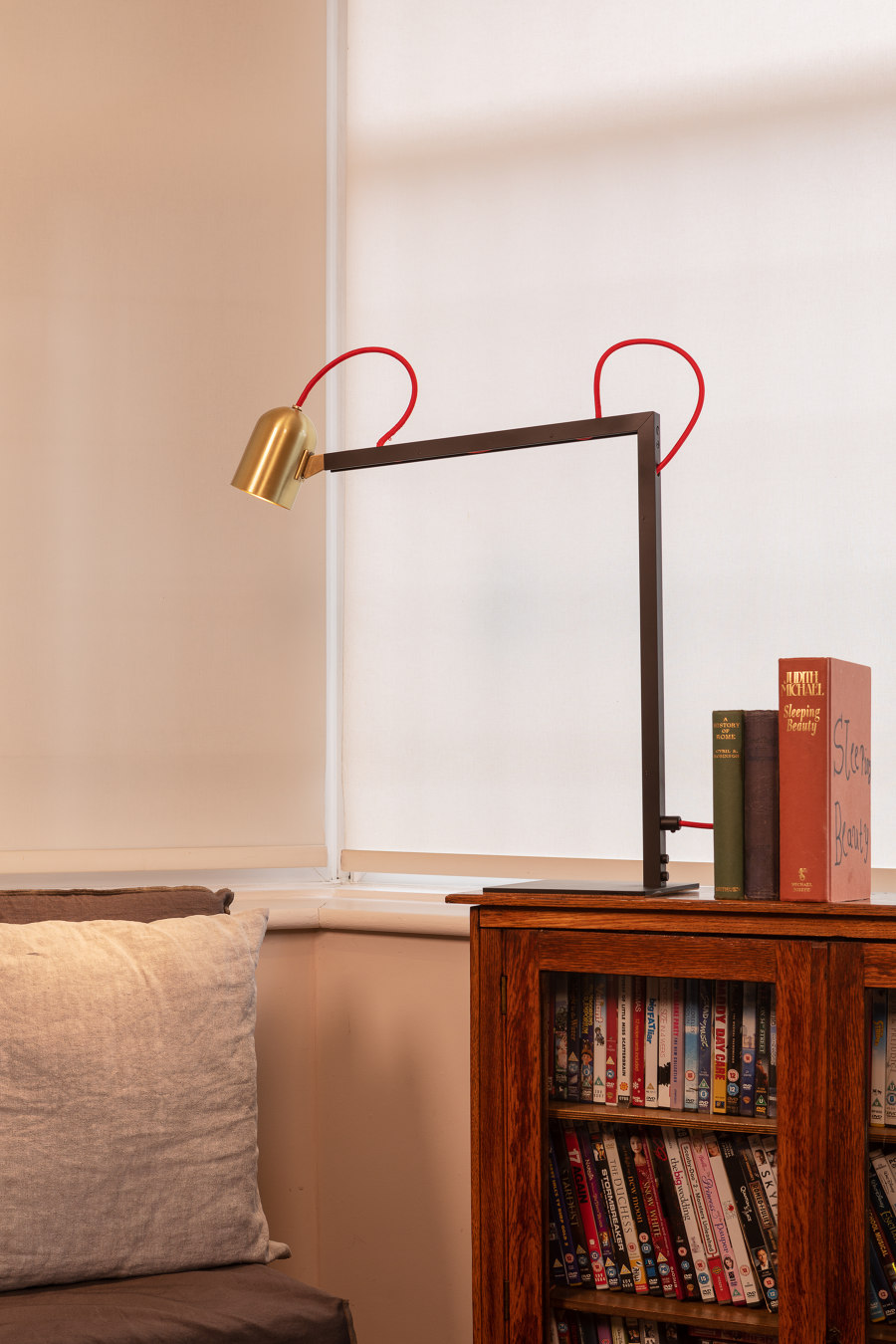
The Lockdown Task Lamp, Joe Scog’s new desk light, was conceived and engineered during the UK’s first lockdown using parts that were available locally or that could be produced easily by hand
×Joe Scog is a nascent British lighting company taking a fresh approach to the design and manufacture of luxury lighting. As an antidote to the industry’s search for ever more original, but often mass-produced design, and the sustainability debate it triggers, Joe Scog sets out to celebrate the skillsets of the engineers and makers that compile its made-to-order lights using hand-made parts and existing components wherever possible. An exercise in producing lighting that is contemporary, polished and high-quality but also waste-free, Joe Scog is addressing sustainability in the lighting industry in a unique way.
Several events conspired to kickstart the company. Like so many brand-initiating moments, the first product came about from a conversation with a friend in need of something they couldn’t find. George Khachfe of West London’s Poliform showroom, a long time business contact of Joe Scog’s industry-insider founder, was ruing the fact that a lighting fixture he had had hanging in the showroom for many years, was consistently the most asked-about feature. It had been made for a display and was not anything its fans could buy.
Joe Scog lamps are designed to meet a specific demand, and made to order. The Lockdown Task Lamp features fine detailing and finishes, some of which can be varied according to taste
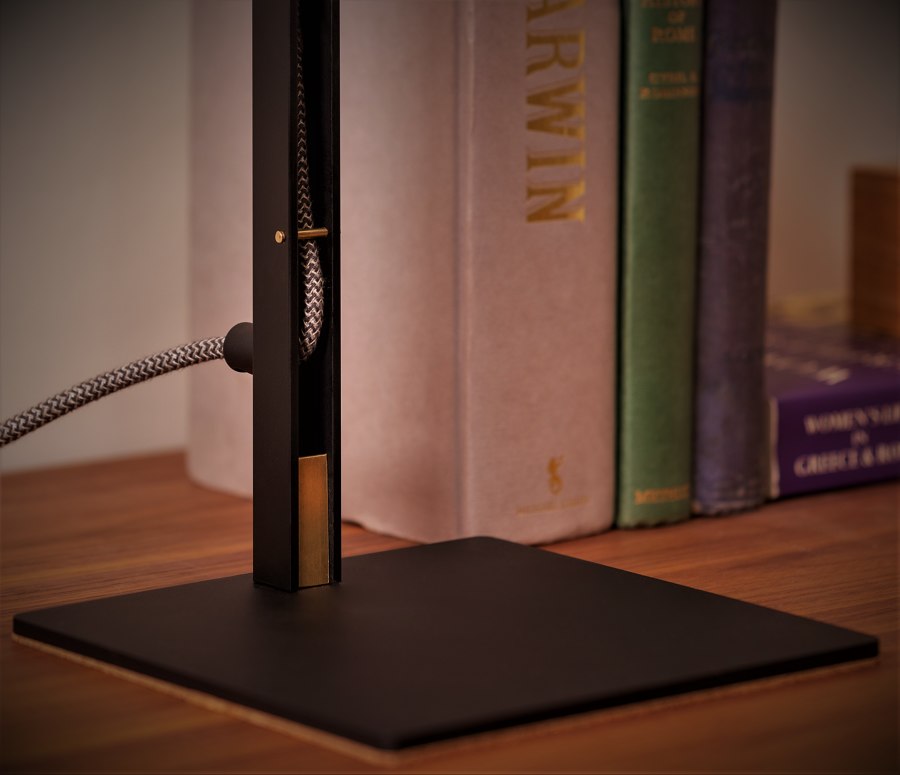
Joe Scog lamps are designed to meet a specific demand, and made to order. The Lockdown Task Lamp features fine detailing and finishes, some of which can be varied according to taste
×With a background in lighting design and engineering, his friend suggested that he could have a go at interpreting the design himself. Replacing the channel of steel for a finely-turned column of triangulated wood, and fixing elegant glass globes at intervals around the column, he succeeded in producing an elegant lighting feature which he named George.
Another light bulb moment came in the halls of Milan’s international design fair, Salone del Mobile, while contemplating the waste that surely comes from creating thousands of new chairs, lighting and storage designs every year. The calculation was made of how much could be done to create desirable pieces of modern lighting, according to demand, using stock parts and handmade components, and working in industry off-cuts when possible. A team was gathered, Joe Scog was founded and the ‘George’ light became the first piece of the collection.
The George pendant was the first piece of lighting the Joe Scog team designed and produced. It is made from solid oak or walnut, brass and hand-blown glass globes for shades
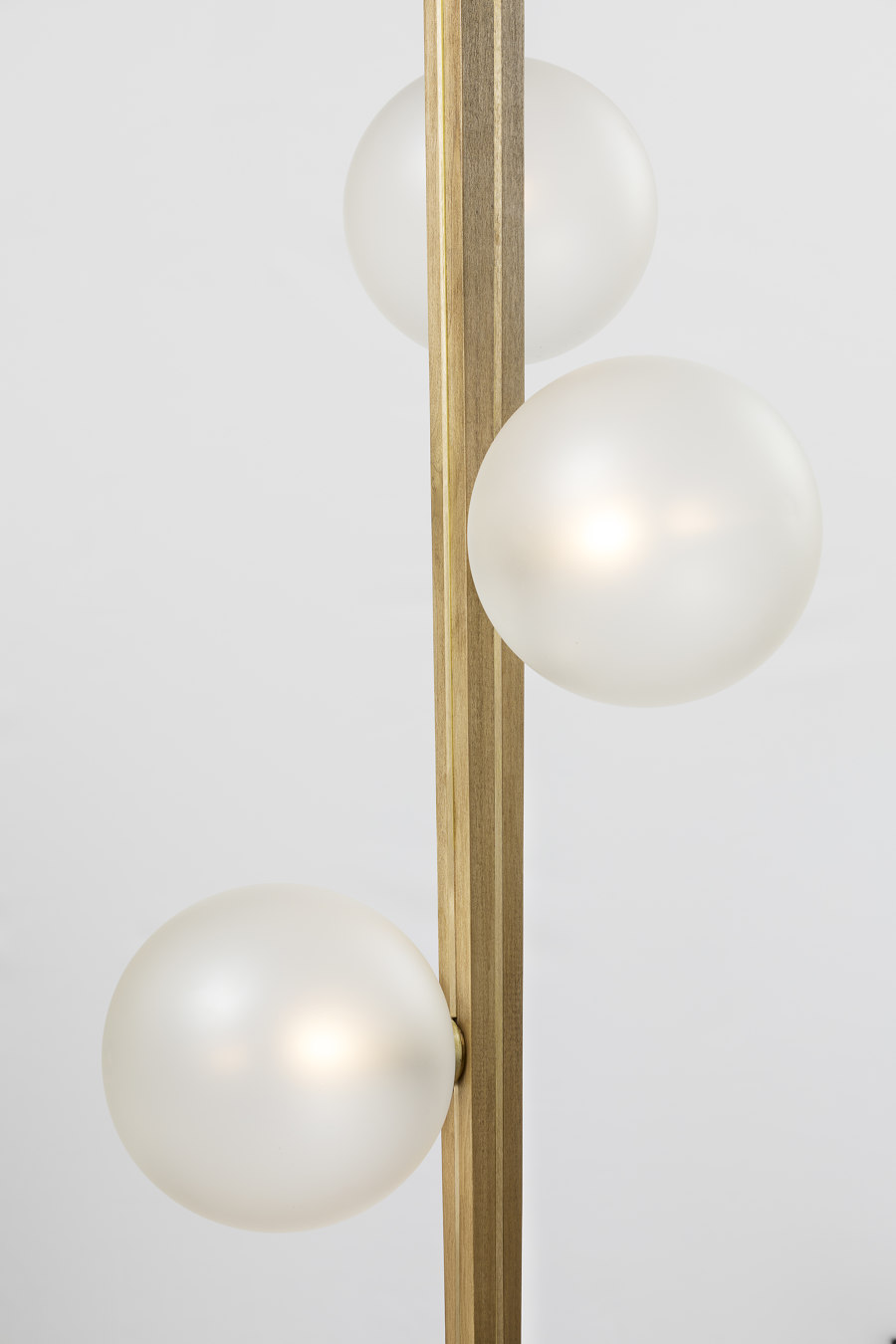
The George pendant was the first piece of lighting the Joe Scog team designed and produced. It is made from solid oak or walnut, brass and hand-blown glass globes for shades
×The company treads a line somewhere between the large-scale production of high-end design and cottage industry. ‘This is a way of producing that takes a step back in time and addresses a need or a request without being dictated by mass production techniques, cost constraints and designers’ egos,’ says the founder who is keen to shine the main light on the engineers and craftspeople behind the lighting pieces and their waste-minimising endeavours. They keep the turning and spinning of new parts to the absolute minimum, and multi-task any they do make across different designs. Forays are currently afoot into the feasibility of buying in reclaimed oak posts and beams to be shaved down for use in the George pendant which is currently made using only FSC-sourced oak and walnut.
Lockdown was the trigger for the design of Joe Scog’s latest light and one that perhaps best embodies the brand’s ethos. One company’s untimely request for ten task lamps during the UK’s first period of pandemic quarantine became Joe Scog’s mission to see what could be done with borders all but closed. Forced to appraise the usefulness of readymade parts available in the UK, Joe Scog handed over the research and engineering of the ‘Lockdown’ task lamp to collaborator Ben Hatton of Iron Oxide Birmingham.
The Guinevere features branched arms made from solid oak or walnut with solid brass details. It can be made to order in a number of different configurations, including tiered arrangements
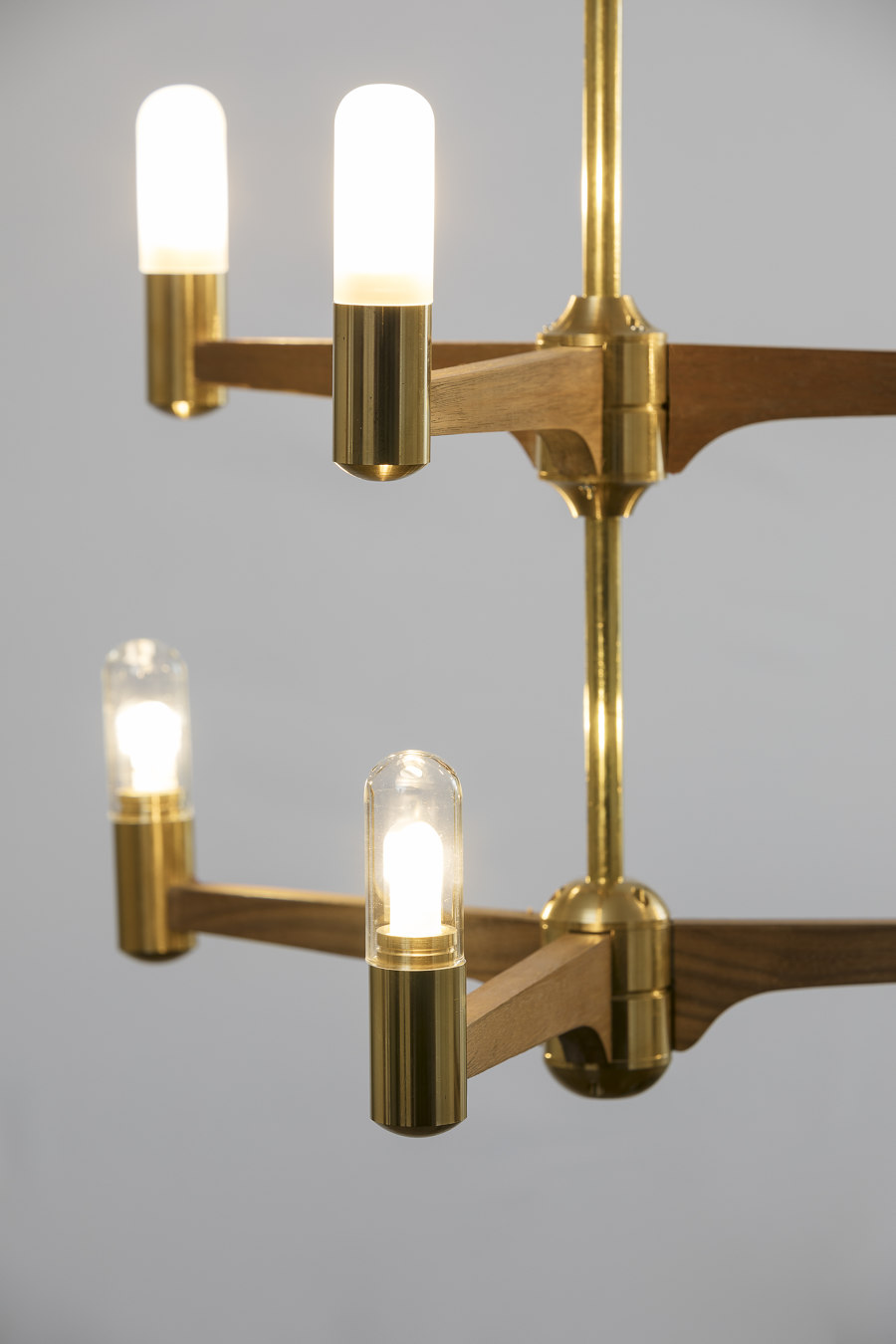
The Guinevere features branched arms made from solid oak or walnut with solid brass details. It can be made to order in a number of different configurations, including tiered arrangements
בThe first four prototypes of the Lockdown light were built using only existing waste materials and some brass components that Joe Scog had already been working with,’ explains Hatton. Indeed, the shade of the articulated lamp is fashioned from the same piece that makes the ceiling rose for the brand’s Guinevere pendant. The basic design for the Lockdown light features a metal base but discarded marble pieces have been sourced to form the bases of a limited number of models.
Where possible, Joe Scog will multi-task components across its lighting designs. The turned brass ceiling rose seen here in the Guinevere pendant has become the shade of the Lockdown Task Lamp
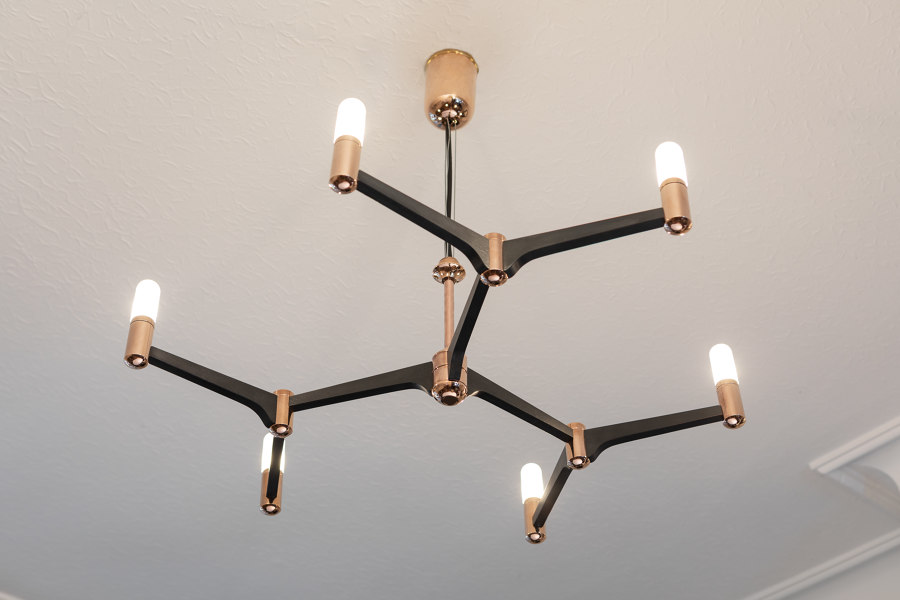
Where possible, Joe Scog will multi-task components across its lighting designs. The turned brass ceiling rose seen here in the Guinevere pendant has become the shade of the Lockdown Task Lamp
×Joe Scog’s engineering-focused formula works because the brand talks the same language as the talented technicians who compose the hardware. ‘We work well together because we both try and push the boundaries of what is and isn’t possible to build using conventional manufacturing processes,’ says Hatton. Rather smartly, Joe Scog has worked out how to justify new design in a world that increasingly interrogates the need for new.
© Architonic