High-Tech meets eco
Scritto da Nora Schmidt
Berlin, Germania
26.11.08
The Swiss designer Beat Karrer researches new processing methods of bio-degradable plastics
There was no lack of euphoria in the last century when plastics and the corresponding industrial processing methods were developed. The world began to light up in all the colours of the rainbow, but few people were able to anticipate the effects which petroleum-based plastics would have on the global eco system in the future.
Today 225 tonnes of plastic are produced every year worldwide. Plastics owe their success above all to their useful properties, because they are easy to mould, durable, and above all cheap. Probably too cheap, because only a small percentage of this material, most of which can be recycled, is actually recovered. Apart from what is today seen as its devastating carbon footprint, plastic also makes a major contribution to global rubbish problems. An obvious example of this is the waste maelstroms which are formed in the oceans by the accumulation of floating rubbish. The biggest of these carpets of waste lies between California and Hawaii and has achieved the size of central Europe.
It is fanciful to imagine that one day all these drifting plastic bags and bottles will suddenly break down and disappear.
As with so many ecological problems there are also materials which could be used as an alternative to plastics - for example, for years now biodegradable plastics have been produced with properties which are almost indistinguishable from traditional plastics. However, because of the lack of demand they are still considerably more expensive. These organic plastics are so-called biopolymers – molecule chains of greater or lesser length which are formed from living organisms, in other words of vegetable (starch, cellulose, pectin), bacterial (polylactic acid) or animal origin (gelatine, wool, silk etc.). They can be supplemented by reinforcing materials such as natural fibre or filling matter.
Different materialities of biopolymeres: sugar-vinegar-composite, starch-salt-water-composite and tapioka-flour-salt-composite. Colour: squeezed blackberries
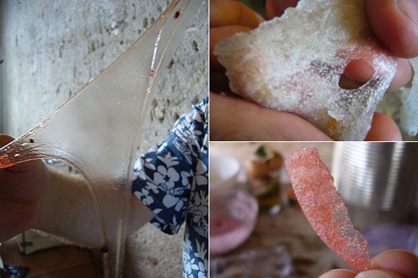
Different materialities of biopolymeres: sugar-vinegar-composite, starch-salt-water-composite and tapioka-flour-salt-composite. Colour: squeezed blackberries
×Stronger ecological awareness and rising oil prices are creating a favourable climate for the increased use of biodegradable plastics, especially for short-lived products such as packaging. Nevertheless the proportion is still pretty small compared to normal plastics.
The Swiss furniture and product designer Beat Karrer has for a long time been researching applications and processing methods for biodegradable plastics. The stimulus for this came from a one-week workshop which Beat Karrer and his team organised with the Vitra Design Museum in Boisbuchet, south of France. The aim was to activate in the participants a playful, uninhibited use of materials, and an awareness of experimental design. Biopolymers which can be from natural raw materials in a few easy stages are especially useful for this approach. The results of the workshop show what impressive production materials can be obtained from organic materials such as starch, protein or cellulose.
Sugar-vinegar-blackberry-composite by Michael Kangas, potatoe-starch is sieved, soaked wheat are squeezed - a gluey paste emerges
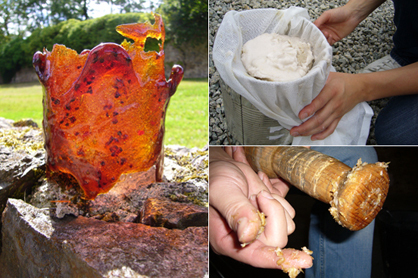
Sugar-vinegar-blackberry-composite by Michael Kangas, potatoe-starch is sieved, soaked wheat are squeezed - a gluey paste emerges
×"These low-tech surroundings in the countryside were just the right place to clear your head and start from scratch. On the first day we began by peeling 30 kilos of potatoes, and cutting them into small pieces. Not to eat them, however, but for the purpose of extracting the starch they contain. In spite of all sustainability considerations, the aspect of competition for raw materials can't be ignored. People all over the world go hungry while we do research into packaging our take-away sushi in bio-plastics made from potato starch" comments Beat Karrer. But in spite of all prophecies of doom, from an ecological point of view continued research in this field is absolutely essential. In cooperation with the biochemist Michael Kangas, who also took part in the Vitra workshop, Karrer is now working on processing methods which can be applied on an industrial scale, such as controlled changes to the material structure of biopolymers. Initial plans are already available. "We're working on the idea of 'programming' the material in such a way that its properties and look and feel are changed in a favourable way by its own energies during the production process. It's a great idea to make a product from biopolymers which creates their own shape within clearly defined parameters. At the moment one of the biggest challenges is controlling the process of degradation. After all, an armchair should biodegrade on a landfill site and not in the living room", concludes the designer.
Peeling potatoes - a fundamental work to extract the starch
Cast made of a sugar-vinegar-composite by Karoline Wicht
'Herb-Cutter-Ring' of the serie ‚products for the herb garden‘ by Runa Klock und Julian Lechner, made of a corn-starch-oil-ater-wool-composite
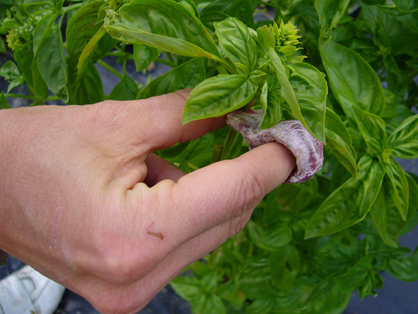
'Herb-Cutter-Ring' of the serie ‚products for the herb garden‘ by Runa Klock und Julian Lechner, made of a corn-starch-oil-ater-wool-composite
×Beat Karrer (left), who organised the workshop in colaboration with the Vitra Design Museum
Initial contacts have already been made with well-known developers of materials, but Karrer is still looking for interested companies which can contribute their know-how to this promising area of research. This wouldn't be the first time that designers were involved in the development of pioneering materials.
Photos by Runa Klock, Tine Kromer, Studio Beat Karrer